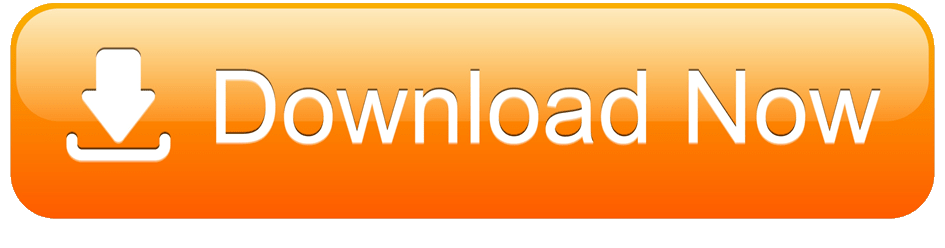
Have a problem with your Jeep Cherokee KJ? Instant download 2002 Jeep Cherokee KJ (also called Jeep Liberty KJ) Service Manual, Fix it! Keep Your Vehicle Running Smoothly.
2002 Jeep Cherokee KJ (also called Jeep Liberty KJ) Service Manual
- Below you will find free PDF files for select years of your Jeep Liberty automobile. 2012 Jeep Liberty Owners Manuals. 2002 Ford Ranger Owner’s Manual.
- 2002 Jeep Liberty Manuals; 2002 Jeep Liberty Repair Manual - Vehicle; Narrow Your Results Brand Chilton (1) Haynes (5) AutoZone Rewards℠ Join Today and Earn a $20 Reward When You Make 5 Purchases of $20 or More! Tell Us More About Your 2002 Jeep Liberty.
2002 Jeep Liberty Service Repair Manuals for factory, Chilton & Haynes service workshop repair manuals. 2002 Jeep Liberty workshop repair manual PDF.
Microsoft Paint for Mac. Apple mac os x. The Gradient tool of the app created for innovative improvements, and it has more similar tools provided in other software.Update: Here in the Modern version of allows you to undo 50 subsequent changes, but in the older version you can do up to three it can also support for all 3D functions.
Instant download a COMPLETE Official Workshop Service and Repair Manual for 2002 Jeep Liberty KJ (Also called Jeep Cherokee outside of North America).
Vehicle Line –
● Liberty 4X2 (LHD)
● Liberty 4X4 (LHD)
● Cherokee 4X4 (RHD)
Kendrick lamar spiteful chant free download. Bully dog triple dog bd-41500 user manual. Serie –
●2002 Jeep Liberty Renegade
●2002 Jeep Liberty Sport
●2002 Jeep Liberty Limited
●2002 Jeep Cherokee Sport
●2002 Jeep Cherokee Limited
Engine –
● 3.7L 6 cyl Gasoline
● 2.4L 4 cyl Gasoline
● 2.5L 4 cyl Diesel
This should work even after the build expires at the end of the month. • Otherwise, you can sign up for the Public Preview on the, and that will automatically send you an email with a link to the newest Public Preview download. Fontlab tab.
This QUALITY manual is 100 percents COMPLETE and INTACT, no MISSING/CORRUPT pages/ sections to freak you out! Buy from responsible seller and get INSTANT DOWNLOAD now without wasting your hard-owned money on uncertainty or surprise; this manual is exactly as described.
GoPro for Mac is categorized as Design & Photo Tools. The actual developer of this free software for Mac is GoPro Inc. The latest installation package that can be downloaded is 177.8 MB in size. Oct 21, 2013 GoPro Studio for Mac is a rather large download at 121MB, but well worth the wait. Once you install it, the application opens with an attractive, intuitive layout that lets you easily import one. Gopro download mac. To install GoPro 2019 For MAC, you will need to install an Android Emulator like Bluestacks or Nox App Player first. With this android emulator app you will be able to Download GoPro full version on your MAC PC and iOS/iPAD. First, Go to this page to Download Bluestacks for MAC. Or Go to this page to Download Nox App Player for MAC.
This is the same type of service manual your local dealer will use when doing a repair. This manual has detailed illustrations as well as step by step instructions. All pages are printable, so run off what you need and take it with you into the garage or workshop. These manuals are your number one source for repair and service information. They are specifically written for the do-it-yourselfer as well as the experienced mechanic. Using this repair manual is an inexpensive way to keep your vehicle working properly. Each manual provides step-by-step instructions based on the complete disassembly of the machine. It is this level of detail, along with hundreds of photos and illustrations, that guide the reader through each service and repair procedure.
2002 Jeep Cherokee KJ Service manual CONTENTS:
■ Introduction
■ Lubrication & Maintenance
■ Suspension
■ Differential & Driveline
■ Brakes
■ Brakes
■ Clutch
■ Cooling
■ Audio
■ Chime/Buzzer
■ Electronic Control Modules
■ Engine Systems
■ Heated Systems
■ Horn
■ Ignition Control
■ Instrument Cluster
■ Lamps
■ Message Systems
■ Power Systems
■ Restraints
■ Speed Control
■ Vehicle Theft Security
■ Wipers/Washers
■ Wiring
■ Engine
■ Exhaust System
■ Frame & Bumpers
■ Fuel System
■ Steering
■ Transmission and Transfer Case
■ Tires/Wheels
■ Body
■ Heating & Air Conditioning
■ Emissions Control
■ Component and System Index
■ 2.4L Gas Component and System Index
PRODUCT DETAILS:
Total Pages: 1791 pages
File Format: PDF (Windows & Mac & Linux)
Mac high sierra frequency software update. 2002 Jeep Cherokee KJ Service manual (2002 Jeep Liberty KJ Service Manual)
Instant Download
Refrigerant Brake Master Cylinder,2002 Jeep Liberty Renegade service manual, Brake Fluid, Brake Booster Brake Actuator, 2002 Jeep Liberty Limited service manual, Body Repair,factory manual Seat Belt Seat, Roof Headlining 2002 Jeep Cherokee Limited service manual, lubrication service, break in procedure, logic box taillight work light indicator lamp, circuit breaker, headlight, resistor module fuel2002 Jeep Cherokee KJ Service manual, Workshop PDF Download, Maintenance Engine Control System Mechanical, Engine Mechanical, Engine Coolant, Engine Control System Emission Control Systems, Drive Shaft, Drive Belt fsm, Camshaft Brake System Brake Pedal,Floor Shift Parking Lock Cable Floor Shift Assy, Fender Panel Mudguard Exhaust Pipe Exhaust Back Door Glass,filter and hoses,Front Suspension Arm, Front Suspension Front Stabilizer 2002 Jeep Liberty KJ Service Manual,Bar Front Speaker Assy, Front Shock Absorber, Front Seat Belt, Front Seat 2002 Jeep Cherokee Sport service manual,Back Door Garnish Back Door, Automatic Transaxle Fluid, repair manual, Automatic Transaxle Assy Audio & Visual System, Antenna Cord Sub-Assy, Amplifier Antenna Assy, storage box, measuring, fuel tank, valve clearance, fender cover, Headlamp Assy, Generator Assy, Fuel Tank, 2002 Jeep Liberty Sport service manual, Fuel System, Fuel Pump, Fuel Injector Front Wheel Alignment, Front Suspension System, Air Conditioning System, Air Conditioning Blower Assy Air Conditioning Amplifier Assy Air Conditioner Airbag Assy, Front Marker Lamp Assy, Front Drive Shaft, Front Door Glass Weatherstrip, Front Door, Front Differential Oil Seal, Front Bumper, Front Brake, Front Axle Hub parts manual Air Bag Sensor Rear Air Bag Sensor Front,Auto Automobile Manual, Factory, Service parts catalog Repair
Related posts:
Page 381 of 1803
HEATED SEAT SENSOR
DIAGNOSIS AND TESTING - HEATED SEAT
SENSOR
For complete circuit diagrams, refer toWIRING.
NOTE: ANY RESISTANCE VALUES (OHMSV) GIVEN
IN THE FOLLOWING TEXT ARE SUPPLIED USING
THE AUTOMATIC RANGE GENERATED BY A
FLUKETAUTOMOTIVE METER. IF ANOTHER TYPE
OF MEASURING DEVICE IS USED THE VALUES
GENERATED MAY NOT BE THE SAME AS THE
RESULTS SHOWN HERE, OR MAY HAVE TO BE
CONVERTED TO THE RANGE USED HERE.
(1) Disconnect the heated seat wire harness con-
nector from under the seat. Using an ohmmeter,
check the resistance between the heated seat sensor
input circuit cavity and the heated seat sensor feed
circuit cavity in the heated seat wire harness connec-
tor. Download mac os on pc without a mac. The heated seat sensor resistance should be
between 1 kilohm and 100 kilohms. If OK, go to Step
2. If not OK, replace the faulty seat heating element
assembly.
(2) Test the seat wire harness between the heated
seat module connector and the heated seat wire har-
ness connector for a shorted or open circuit. If OK,
refer toDiagnosis and Testing the Heated Seat
Modulein Electronic Control Modules, for the
proper heated seat module diagnosis and testing pro-
cedures. If not OK, repair the shorted or open heated
seat wire harness as required.
PASSENGER SEAT HEATER
SWITCH
DESCRIPTION
The heated seat switches are located on the out-
board cushion side shield of the driver and passenger
front seats (Fig. 3). The two, three-position rocker
type switches provide a resistor multiplexed signal to
the Heated Seat Module through separate hard wired
circuits. Each switch has an Off, Low and High set-
ting. Each switch contains two light emitting diodes
(LED), one for each High and Low setting to let the
occupant know that the seat heater system is on.
The heated seat switches and their LED's cannot
be repaired. If either switch is faulty or damaged the
entire switch must be replaced.
OPERATION
There are three positions that can be selected with
each of the heated seat switches: Off, Low, and High.
When the front of the switch rocker is fullydepressed, the High position is selected and the high
position LED indicator illuminates. When the rear of
the switch rocker is fully depressed, the Low position
is selected and the low position LED indicator illumi-
nates. When the switch rocker is depressed a second
time in either direction, Off is selected and both LED
indicators are extinguished.
Both switches provide separate resistor multi-
plexed hard wire inputs to the Heated Seat Module
to indicate the selected switch position. The heated
seat module monitors the switch inputs and responds
to the heated seat switch status messages by control-
ling the output to the seat heater elements of the
selected seat. The Low heat position set point is
about 36É C (97É F), and the High heat position set
point is about 41É C (105É F).
DIAGNOSIS AND TESTING - HEATED SEAT
SWITCH
If a heated seat fails to heat and one or both of the
indicator lamps on a heated seat switch flash, refer
toHeated Seat System Diagnosis and Testingin
this section for flashing LED failure identification.
Refer toWiring Diagramsfor complete heated seat
system wiring diagrams.
(1) If the problem being diagnosed involves a
heated seat switch indicator lamp that remains illu-
minated after the heated seat has been turned Off,
refer toDiagnosis and Testing the Heated Seat
Modulein the Electronic Control Modules section for
heated seat module diagnosis and testing procedures.
If not, go to Step 2
Fig. 3 KJ POWER / HEATED SEAT
8G - 14 HEATED SEAT SYSTEMKJ
Page 382 of 1803
(2) Remove the heated seat switch (Refer to 8 -
ELECTRICAL/HEATED SEATS/DRIVER HEATED
SEAT SWITCH - REMOVAL). Check for continuity
between the ground circuit cavity #5 of the heated
seat switch connector and a good ground. There
should be continuity. If OK, go to Step 3. If not OK,
repair the open ground circuit as required.
(3) Turn the ignition switch to the ON position.
Check for battery voltage at the fused ignition switch
output circuit cavity #1 of the heated seat switch con-
nector. If OK, go to Step 4. If not OK, repair the open
fused ignition switch output circuit as required.
(4) Check the continuity between pin #1 and pin
#3 of the heated seat switch (Fig. 4). If the readings
do not correspond to those in the Heated Seat Switch
Continuity table below, replace the heated seat
switch. If OK, and the heated seat system is still not
operating properly refer toDiagnosis and Testing
the Heated Seat Module.NOTE: ANY RESISTANCE VALUES (OHMSV) GIVEN
IN THE FOLLOWING TEXT ARE SUPPLIED USING
THE AUTOMATIC RANGE GENERATED BY A
FLUKETAUTOMOTIVE METER. IF ANOTHER TYPE
OF MEASURING DEVICE IS USED, THE VALUES
GENERATED MAY NOT BE THE SAME AS THE
RESULTS SHOWN HERE, OR MAY HAVE TO BE
CONVERTED TO THE RANGE USED HERE.
HEATED SEAT SWITCH CONTINUITY
CONTINUITY
BETWEENSWITCH
POSITIONOHMS
READING +/±
10%
PIN 1 AND 3 OFF 2.2 K (2200)
OHMS
PIN 1 AND 3 LO .415 K (415)
OHMS
PIN 1 AND 3 HI 33 OHMS
REMOVAL
(1) Disconnect and isolate the negative battery
cable.
(2) Remove the appropriate seat cushion side
shield (Refer to 23 - BODY/SEATS/SEAT CUSHION
SIDE COVERS - REMOVAL).
(3) Disconnect the heated seat switch electrical
connector. Depress the locking tab and pull straight
apart.
(4) Working from the underside of the switch, gen-
tly rock the switch back and forth out of its mounting
location.
INSTALLATION
(1) Gently rock the switch back and forth in to its
mounting location.
(2) Connect the heated seat switch electrical con-
nector.
(3) Install the appropriate seat cushion side shield.
Refer to the Body section of the service manual for
the procedure.
(4) Connect the negative battery cable.
Fig. 4 Heated Seat Switches
KJHEATED SEAT SYSTEM 8G - 15
PASSENGER SEAT HEATER SWITCH (Continued)
Page 383 of 1803
Page 384 of 1803
HORN
TABLE OF CONTENTS
page page
HORN SYSTEM
DESCRIPTION.......1
OPERATION.......1
DIAGNOSIS AND TESTING - HORN SYSTEM . . . 1
HORN
DIAGNOSIS AND TESTING - HORN...2
REMOVAL........3
INSTALLATION.......3HORN RELAY
DIAGNOSIS AND TESTING - HORN RELAY.3
REMOVAL........3
INSTALLATION.......3
HORN SWITCH
DESCRIPTION.......4
DIAGNOSIS AND TESTING - HORN SWITCH . . . 4
HORN SYSTEM
DESCRIPTION
A dual-note electric horn system is standard facto-
ry-installed equipment on this model (Fig. 1).
The dual-note horn system features dual electro-
magnetic horn units. The horn system includes the
following major components:
²Horn- The two horns are located below the
Power Distribution Center (PDC).
²Horn Relay- The horn relay is located in the
Junction Block (JB).²Horn Switch- The horn switch is molded into
the driver airbag assembly.OPERATION
The horn system operates on battery current
received through fuse 3 in the Junction Block (JB).
The horn system circuit is designed so that the sys-
tem will remain operational, regardless of the igni-
tion switch position.
DIAGNOSIS AND TESTING - HORN SYSTEM
In most cases, any problem involving continually
sounding horns can be quickly alleviated by removing
the horn relay from the Junction Block (JB). Refer to
horn relay for the removal procedure. Refer to the
appropriate wiring information. The wiring informa-
tion includes wiring diagrams, proper wire and con-
nector repair procedures, further details on wire
harness routing and retention, as well as pin-out and
location views for the various wire harness connec-
tors, splices and grounds.
WARNING: DISABLE THE AIRBAG SYSTEM
BEFORE ATTEMPTING ANY STEERING WHEEL,
STEERING COLUMN, SEAT BELT TENSIONER, SIDE
AIRBAG, OR INSTRUMENT PANEL COMPONENT
DIAGNOSIS OR SERVICE. DISCONNECT AND ISO-
LATE THE BATTERY NEGATIVE (GROUND) CABLE,
THEN WAIT TWO MINUTES FOR THE AIRBAG SYS-
TEM CAPACITOR TO DISCHARGE BEFORE PER-
FORMING FURTHER DIAGNOSIS OR SERVICE. THIS
IS THE ONLY SURE WAY TO DISABLE THE AIRBAG
SYSTEM. FAILURE TO TAKE THE PROPER PRE-
CAUTIONS COULD RESULT IN ACCIDENTAL AIR-
BAG DEPLOYMENT AND POSSIBLE PERSONAL
INJURY.
Fig. 1 HORN LOCATION
1 - HIGH NOTE HORN
2 - LOW NOTE HORN
KJHORN 8H - 1
https://treeip642.weebly.com/blog/roxio-easy-vhs-to-dvd-for-mac. We want you to be satisfied with your Micro Center purchase. Micro Center Return Policy:We guarantee your satisfaction on every product we sell with a full refund — and you won’t even need a receipt.
Page 385 of 1803
HORN SYSTEM DIAGNOSIS TABLE
CONDITION POSSIBLE CAUSES CORRECTION
BOTH HORNS
INOPERATIVE1. Faulty fuse. 1. Check the fuse in the Junction Block (JB).
Replace the fuse and repair the shorted circuit or
component, if required.
2. Faulty horn relay. 2. Refer to horn relay for the proper diagnosis
and testing procedures. Replace the horn relay or
repair the open horn relay circuit, if required.
3. Faulty horn switch. 3. Refer to horn switch for the proper diagnosis
and testing procedure. Replace the horn switch or
repair the open horn switch circuit, if required.
4. Faulty horns. 4. Refer to horn for the proper diagnosis and
testing procedure. Replace the horns or repair the
open horn circuit, if required.
ONE HORN INOPERATIVE 1. Faulty horn. 1. Refer to horn for the proper diagnosis and
testing procedures. Replace the horn or repair the
open horn circuit, if required.
HORN SOUNDS
CONTINUOUSLY1. Faulty horn relay. 1. Refer to horn relay for the proper diagnosis
and testing procedure. Replace the horn relay or
repair the shorted horn relay control circuit, if
required.
2. Faulty horn switch. 2. Refer to horn switch for the proper diagnosis
and testing procedure. Replace the horn switch or
repair the shorted horn switch circuit, if required.
HORN
DIAGNOSIS AND TESTING - HORN
WARNING: DISABLE THE AIRBAG SYSTEM
BEFORE ATTEMPTING ANY STEERING WHEEL,
STEERING COLUMN, SEAT BELT TENSIONER, SIDE
AIRBAG, OR INSTRUMENT PANEL COMPONENT
DIAGNOSIS OR SERVICE. DISCONNECT AND ISO-
LATE THE BATTERY NEGATIVE (GROUND) CABLE,
THEN WAIT TWO MINUTES FOR THE AIRBAG SYS-
TEM CAPACITOR TO DISCHARGE BEFORE PER-
FORMING FURTHER DIAGNOSIS OR SERVICE. THIS
IS THE ONLY SURE WAY TO DISABLE THE AIRBAG
SYSTEM. FAILURE TO TAKE THE PROPER PRE-
CAUTIONS COULD RESULT IN ACCIDENTAL AIR-
BAG DEPLOYMENT AND POSSIBLE PERSONAL
INJURY.
Refer to the appropriate wiring information. The
wiring information includes wiring diagrams, proper
wire and connector repair procedures, further details
on wire harness routing and retention, as well as
pin-out and location views for the various wire har-
ness connectors, splices and grounds.(1) Disconnect the wire harness connector from the
horn. Measure the resistance between the horn
ground circuit cavity of the wire harness connector
and a good ground. There should be no measurable
resistance. If OK, go to Step 2. If not OK, replace
wiring as necessary.
(2) Check for battery voltage at the horn relay out-
put circuit cavity of the wire harness connector for
the horn. There should be zero volts. If OK, go to
Step 3. If not OK, refer to horn relay and horn relay
circuit for the proper diagnosis and testing proce-
dures.
(3) Depress the horn switch. There should now be
battery voltage at the horn relay output circuit cavity
of the wire harness connector for the horn. If OK, but
the horn does not sound, replace the faulty horn. If
not OK, refer to horn relay and horn relay circuit for
the proper diagnosis and testing procedures.
8H - 2 HORNKJ
HORN SYSTEM (Continued)
Page 386 of 1803
REMOVAL
(1)Disconnect and isolate the battery negative cable.
(2) Disconnect the electrical harness connector
from the horns.
(3) Remove the mounting bolt (Fig. 2).
(4) Remove the horns.
INSTALLATION
(1) Install the horns.
(2) Install the mounting bolt. Tighten bolt to 25
N´m (19 lb. ft.).
(3) Connect the electrical harness connector to the
horns
(4) Connect the battery negative cable.
HORN RELAY
DIAGNOSIS AND TESTING - HORN RELAY
(1) Remove horn relay (Refer to 8 - ELECTRICAL/
HORN/HORN RELAY - REMOVAL).
(2) Using ohmmeter, test between relay connector
terminals 85 to 86 for 75 8 ohms resistance. If
resistance not OK, replace relay (Fig. 3).
(3) Test for continuity between ground and termi-
nal 85 of horn relay.
(a) When the horn switch is not depressed, no
continuity should be present.
(b) Continuity to ground when horn switch is
depressed.
(c) If continuity is not correct replace horn
switch or wiring as necessary, refer to the appro-
priate wiring information. The wiring information
includes wiring diagrams, proper wire and connec-
tor repair procedures, details of wire harness rout-ing and retention, connector pin-out information
and location views for the various wire harness
connectors, splices and grounds.
(4) Using voltmeter, test voltage at:
(a) Terminals 30 and 86 of the horn relay to
body ground.
(b) If NO voltage check fuse 3 of the Junction
Block (JB).
(c) If incorrect voltage, repair as necessary. Refer
to the appropriate wiring information. The wiring
information includes wiring diagrams, proper wire
and connector repair procedures, details of wire
harness routing and retention, connector pin-out
information and location views for the various wire
harness connectors, splices and grounds.
(5) Insert a jumper wire between terminal 30 and
87 of the Junction Block (JB).
(a) If horn sounds replace relay.
(b) If the horn does not sound, install horn relay
and test horn (Refer to 8 - ELECTRICAL/HORN/
HORN - DIAGNOSIS AND TESTING).
REMOVAL
(1) Disconnect and isolate the battery negative
cable.
(2) Remove the instrument panel end cap.
(3) Locate and pull the horn relay from the Junc-
tion Block (JB).
INSTALLATION
(1) Locate proper connector, and press relay into
position.
(2) Install instrument panel end cap.
(3) Connect battery negative cable.
Fig. 2 HORN MOUNTING
1 - POWER DISTRIBUTION CENTER
2 - LOW NOTE HORN
3 - HIGH NOTE HORN
Fig. 3 Horn Relay
30 - COMMON FEED
85 - COIL GROUND
86 - COIL BATTERY
87 - NORMALLY OPEN
87A - NORMALLY CLOSED
KJHORN 8H - 3
HORN (Continued)
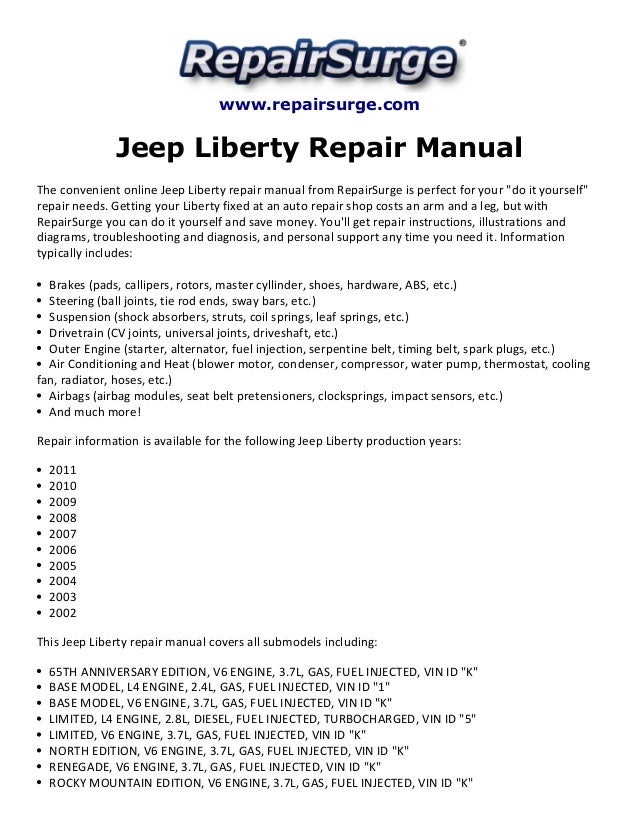
Page 387 of 1803
HORN SWITCH
DESCRIPTION
The horn switch is molded into the driver airbag
assembly. The horn switch can not be serviced sepa-
rately. For service procedures, (Refer to 8 - ELEC-
TRICAL/RESTRAINTS/DRIVER AIRBAG -
REMOVAL).
DIAGNOSIS AND TESTING - HORN SWITCH
For complete circuit diagrams, refer to the appro-
priate wiring information. The wiring information
includes wiring diagrams, proper wire and connector
repair procedures, details of wire harness routing
and retention, connector pin-out information and
location views for the various wire harness connec-
tors, splices and grounds.
WARNING: DISABLE THE AIRBAG SYSTEM
BEFORE ATTEMPTING ANY STEERING WHEEL,
STEERING COLUMN, SEAT BELT TENSIONER, SIDE
AIRBAG, OR INSTRUMENT PANEL COMPONENT
DIAGNOSIS OR SERVICE. DISCONNECT AND ISO-
LATE THE BATTERY NEGATIVE (GROUND) CABLE,
THEN WAIT TWO MINUTES FOR THE AIRBAG SYS-
TEM CAPACITOR TO DISCHARGE BEFORE PER-
FORMING FURTHER DIAGNOSIS OR SERVICE. THIS
IS THE ONLY SURE WAY TO DISABLE THE AIRBAG
SYSTEM. FAILURE TO TAKE THE PROPER PRE-
CAUTIONS COULD RESULT IN ACCIDENTAL AIR-
BAG DEPLOYMENT AND POSSIBLE PERSONAL
INJURY.
(1) Disconnect and isolate the battery negative
cable.
(2) Remove the steering column opening cover.
(3) Check for continuity between the metal steer-
ing column jacket and a good ground. There should
be continuity. If OK, go to Step 4. If not OK,(Refer to
19 - STEERING/COLUMN - INSTALLATION) for
proper installation of the steering column.
(4) Remove the driver side airbag module from the
steering wheel (Refer to 8 - ELECTRICAL/RE-
STRAINTS/DRIVER AIRBAG - REMOVAL). Discon-
nect the horn switch wire harness connectors from
the driver side airbag module (Fig. 4).
(5) Remove the horn relay from the Junction Block
(JB). Check for continuity between the steering col-umn half of the horn switch feed wire harness con-
nector and a good ground. There should be no
continuity. If OK, go to Step 6. If not OK, repair the
shorted horn relay control circuit to the horn relay in
the Junction Block as required.
(6) Check for continuity between the steering col-
umn half of the horn switch feed wire harness con-
nector and the horn relay control circuit cavity for
the horn relay in the Junction Block. There should be
continuity. If OK, go to Step 7. If not OK, repair the
open horn relay control circuit to the horn relay in
the Junction Block as required.
(7) Check for continuity between the horn switch
feed wire and the horn switch ground wire on the
driver side airbag module. There should be no conti-
nuity. If OK, go to Step 8. If not OK, replace the
faulty horn switch.
(8) Depress the center of the driver side airbag
module trim cover and check for continuity between
the horn switch feed wire and the horn switch
ground wire on the driver side airbag module. There
should now be continuity. If not OK, replace the
faulty horn switch (Refer to 8 - ELECTRICAL/RE-
STRAINTS/DRIVER AIRBAG - REMOVAL).
Fig. 4 Driver Airbag Housing
1 - HOUSING
2 - HORN SWITCH GROUND WIRE
3 - HORN SWITCH FEED WIRE
4 - INFLATOR
5 - TRIM COVER
8H - 4 HORNKJ
Novell (2). Apc smart ups 5000 user manual online. Microsoft Hyper-V (4). Nutanix (1). Mac OS X (3). Red Hat Enterprise Linux (1).
Page 388 of 1803
IGNITION CONTROL
TABLE OF CONTENTS
page page
IGNITION CONTROL
DESCRIPTION.......1
OPERATION.......1
SPECIFICATIONS
SPECIFICATIONS - IGNITION TIMING..2
ENGINE FIRING ORDER - 2.4L 4-CYLINDER . 2
ENGINE FIRING ORDER - 3.7L V-6...2
IGNITION COIL RESISTANCE - 2.4L..2
IGNITION COIL RESISTANCE - 3.7L V-6..3
SPARK PLUGS......3
SPARK PLUG CABLE RESISTANCE - 2.4L . . . 3
TORQUE - IGNITION SYSTEM...3
AUTO SHUT DOWN RELAY
DESCRIPTION - PCM OUTPUT....4
OPERATION
OPERATION - ASD SENSE - PCM INPUT.4
OPERATION - PCM OUTPUT....4
DIAGNOSIS AND TESTING - ASD AND FUEL
PUMP RELAYS......4
REMOVAL........5
INSTALLATION.......5
CAMSHAFT POSITION SENSOR
DESCRIPTION
DESCRIPTION - 2.4L.....5
DESCRIPTION-3.7L......6
OPERATION
OPERATION - 2.4L......6OPERATION - 3.7L......6
REMOVAL........7
INSTALLATION.......8
IGNITION COIL
DESCRIPTION.......9
OPERATION.......9
REMOVAL........10
INSTALLATION.......10
KNOCK SENSOR
DESCRIPTION.......11
OPERATION.......11
REMOVAL........12
INSTALLATION.......12
SPARK PLUG
DESCRIPTION.......12
OPERATION.......12
DIAGNOSIS AND TESTING - SPARK PLUG
CONDITIONS.......13
REMOVAL........15
CLEANING SPARK PLUGS....15
INSTALLATION.......15
IGNITION COIL CAPACITOR
DESCRIPTION.......16
OPERATION.......16
REMOVAL........16
INSTALLATION.......16
IGNITION CONTROL
DESCRIPTION
The ignition system consists of:
²Spark Plugs
²Ignition Coil(s)
²Powertrain Control Module (PCM)
²Crankshaft Position Sensor
²2 Knock Sensors (3.7L only)
²Camshaft Position Sensor
²The MAP, TPS, IAC and ECT also have an effect
on the control of the ignition system.
OPERATION
2.4L
A common ignition coil divided into 2 halves is
used. Secondary, high-tension spark plug cables are
also used. One half of the coil fires two spark plugs
simultaneously (one plug is the cylinder under com-pression, and the other plug is the cylinder on the
exhaust stroke). Coil half number one fires cylinders
1 and 4. Coil half number two fires cylinders 2 and 3.
The PCM determines which of the coils to charge and
fire at the correct time.
The Auto Shutdown (ASD) relay provides battery
voltage to the ignition coil. The PCM provides a
ground contact (circuit) for energizing the coil. When
the PCM breaks the contact, the energy in the coil
primary transfers to the secondary causing a spark.
The PCM will de-energize the ASD relay if it does
not receive inputs from either the crankshaft or cam-
shaft position sensors.
A distributor is not used with the 2.4L engine.
3.7L
The 3.7L V6 engine uses a separate ignition coil for
each cylinder. The one-piece coil bolts directly to the
cylinder head. Rubber boots seal the secondary ter-
minal ends of the coils to the top of all 6 spark plugs.
A separate electrical connector is used for each coil.
KJIGNITION CONTROL 8I - 1
Page 389 of 1803
Because of coil design, spark plug cables (second-
ary cables) are not used. A distributor is not used
with the 3.7L engine.
Two knock sensors (one for each cylinder bank) are
used to help control spark knock.
The Auto Shutdown (ASD) relay provides battery
voltage to each ignition coil. The Powertrain Control
Module (PCM) provides a ground contact (circuit) for
energizing each coil. When the PCM breaks the con-
tact, the energy in the coil primary transfers to the
secondary causing a spark. The PCM will de-energize
the ASD relay if it does not receive inputs from
either the crankshaft or camshaft position sensors.
SPECIFICATIONS
SPECIFICATIONS - IGNITION TIMING
Ignition timing is not adjustable on any
engine.
ENGINE FIRING ORDER - 2.4L 4-CYLINDER1-3-4-2
ENGINE FIRING ORDER - 3.7L V-61-6-5-4-3-2
IGNITION COIL RESISTANCE - 2.4L
Engine Coil ManufacturePrimary Resistance at
21ÉC-27ÉC (70ÉF-80ÉF)Secondary Resistance at
21ÉC-27ÉC (70ÉF-80ÉF)
2.4L Toyodenso or Diamond 0.51 to 0.61 Ohms 11,500 to 13,500 Ohms
Fig. 1 IGNITION COIL - 2.4L
8I - 2 IGNITION CONTROLKJ
IGNITION CONTROL (Continued)
Jeep Liberty 2002 User Manual Pdf 2 8
Page 390 of 1803
IGNITION COIL RESISTANCE - 3.7L V-6
PRIMARY RESISTANCE
21-27ÉC (70-80ÉF)SECONDARY
RESISTANCE 21-27ÉC
(70-80ÉF)
0.6 - 0.9 Ohms 6,000 - 9,000 Ohms
SPARK PLUGS
ENGINE PLUG TYPE ELECTRODE GAP
2.4L RE14MCC5 (Champion #) 1.24 to 1.37 mm (0.048 to 0.053 in.)
3.7L V-6 2FR6F - 11G (NGK #) 1.1 mm (0.042 in.)
SPARK PLUG CABLE RESISTANCE - 2.4L
MINIMUM MAXIMUM
250 Ohms Per Inch 1000 Ohms Per Inch
3000 Ohms Per Foot 12,000 Ohms Per Foot
TORQUE - IGNITION SYSTEM
DESCRIPTION N-m Ft. Lbs. In. Lbs.
Camshaft Position Sensor-2.4L 23 21 205
Camshaft Position Sensor±3.7L 12 - 106
Crankshaft Position Sensor Bolt-2.4L 12 - 106
Crankshaft Position Sensor Nut/Bolt-3.7L 23 21 205
* Knock Sensor Bolt - 3.7L * 20 * 15
Ignition Coil Mounting Bolts - 2.4L 11 - 105
Ignition Coil Mounting Nuts - 3.7L 8 - 70
Ignition Coil Capacitor Nuts- 3.7L 8 - 70
** Spark Plugs - 2.4L ** 15 ** 11 -
Spark Plugs - 3.7L 27 20 -
* Do not apply any sealant, thread-locker or adhesive to
bolts. Poor sensor performance may result.
** Torque critical tapered design. Do not exceed 15 ft. lbs.
KJIGNITION CONTROL 8I - 3
IGNITION CONTROL (Continued)
User Manual
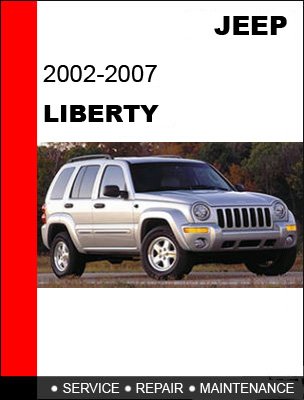
Instruction Manual
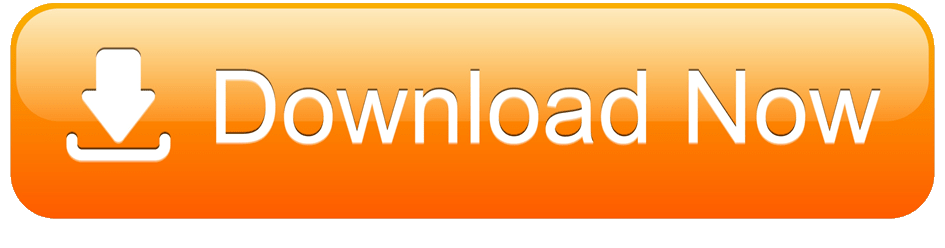